make Refined quartz sand When iron removal is a major thing, how to remove iron reasonably and effectively? refined Quartz sand It is a major mineral raw material for industrial production. Its appearance is grayish white or crystalline, and it is widely used in laminated glass, casting, porcelain and refractory insulation materials, metallurgical industry, engineering buildings, chemical plants, plastics, rubber, wear-resistant materials and other industrial production. During the production of refined quartz sand, iron must be removed at a deep level, which is a very critical process, mainly to improve the content of quartz sand. So what can be done to remove iron under the condition of producing refined quartz sand?
In the production of refined quartz sand, generally speaking, there are three ways of iron removal: mechanical equipment wiping iron removal, magnetic separation equipment iron removal and ultrasonic wave iron removal.
The iron removal by mechanical equipment wiping is mainly to remove the iron residue outside the quartz sand raw ore according to the effect of external force. There are two kinds of mechanical equipment wiping: rod mill wiping and mechanical equipment wiping. When using mechanical equipment to remove iron, some aqueous solutions are also required to cooperate with each other, and the concentration value of coal slurry is set to a certain ratio to remove iron from raw ore quartz sand. However, this kind of iron removal method is only applicable to some manufacturers with small production capacity or under the condition that the quality of raw quartz sand is very good
The magnetic separation equipment removes iron according to the chemical properties of iron. The magnetic separation equipment has two methods, dry separation and wet separation, each of which has its own advantages. When it is used, the composition of raw quartz sand should be measured as far as possible. If the raw quartz sand contains hematite, limonite, biotite and other weak magnetic residues with intergrowth particles in it, the wet separation is the only way, However, the disadvantages of wet separation are large power consumption, easily damaged materials, large water demand for production, and high operation and maintenance costs. If the above residues are not available, dry separation can be used. Compared with wet separation, the cost and maintenance are extremely low;
It is ultrasonic iron removal. This kind of method is mainly used to remove the secondary cast iron plastic film on the surface of particles. The way of cleaning mechanical equipment is not good.
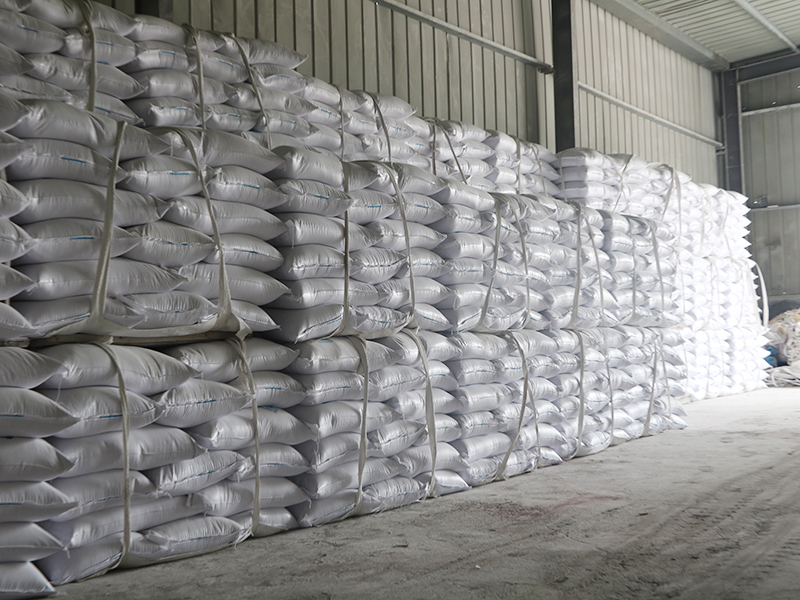