stay Heavy calcium carbonate What are the technical indicators concerned in the application?
I Pure white sand Gloss: whiteness is mainly related to the origin of calcium carbonate magnesite, the composition of iron ore, and the type of iron ore. Generally speaking, the higher the glossiness is, the higher the calcium carbonate content is. The glossiness is critical to the glossiness, smoothness and colourability of plastic products. There is also a common problem of color in glossiness, because calcium carbonate magnesite contains some other elements, and the color of calcium carbonate from different places of origin is also generally different, the key is red phase, gray phase, and dark color.
2、 Particle size and particle size analysis: particle size refers to the size of particles. Particle size analysis refers to the proportion of particles of various sizes in the number of particles in the powder sample. It is common for people to use "screen mesh number" to indicate the fineness of the powder, and D97 is used to indicate the relative particle size. However, a simple D97 does not mean the fineness characteristics of the powder, and a complete particle size layout should be used to show the fineness characteristics. In plastic products, the narrower the scope of calcium carbonate particle size analysis, the more stable the production, processing and product quality; The wider the particle size analysis is, the more difficult the production and processing are, and the product quality is unstable.
3、 Specific surface area: the specific surface area of the powder sample refers to the sum of the areas of all particles in the sample of enterprise quality. Generally speaking, the finer the fineness, the larger the specific surface area. However, the composition of coarse powder and stone powder should also be considered. If the composition of stone powder is high, but its D97 standard value is relatively large, the condition of large fineness and large specific surface area will occur. At the same time, when judging the specific surface area, the surface appearance of particles and whether particles are solid should also be considered. If there are many holes or dents on the surface of particles, the measured specific surface area is also high. Generally, the larger the specific surface area, the higher the smoothness of the product, but its dispersion is also difficult.
4、 Residual oil absorption: the amount of oil absorption refers to the amount of dioctyl phthalate (DOP) digested and absorbed by 100g powder. In production, processing and application, it is expected that the lower the residual oil absorption is, the better. The lower the amount of oil absorption, the lower the amount of digesting and absorbing viscosifier, and the lower the cost. Generally, the finer the powder particles are, the greater the residual oil absorption.
5、 False proportion: False proportion is usually called apparent density or loose relative density. In a practical sense, false proportion also reflects the fineness of powder. It is considered to be the main index value for everyone to distinguish the fineness of powder in combination with D97, specific surface area and particle size analysis.
6、 Particle appearance: Due to the difference in production equipment, original ore origin and crystal structure, heavy calcium carbonate is usually divided into various particle shapes, such as multi-faceted body, flat flat body, rectangle, long rod, near round ball and irregular shape. In many aspects, the rectangular calcium carbonate has good circulation in the processing of plastic products, which is convenient for silane coupling agent to cover chemical crosslinking, and the production equipment is less damaged, but the physical properties of the product are relatively reduced; The specific surface area of flat flat and long rod particles is relatively large. If surface treatment is carried out, the silane coupling dose will be increased, but the physical properties of the product are good.
7、 Activity of surface treated heavy calcium: surface treated heavy calcium is also called active heavy calcium. In order to better improve its fusion with the raw materials of the base material and enhance its dispersivity, it is necessary to solve its activity. For heavy calcium manufacturing enterprises, surface treatment of calcium carbonate is the main way of commodity production and processing, which can enhance the added value and obtain faster economic benefits. However, for the active calcium carbonate and the following customers, the active calcium carbonate should be used, followed by heavy calcium, which is usually solved by physical covering or organic chemical mechanical equipment to modify materials. Its working principle and the whole process are different from the anti condensation solution of carbonization in the production process of light calcium. In order to better show the actual effect of heavy calcium activity solution, we often use the index value of activity to show the actual effect of surface treatment.
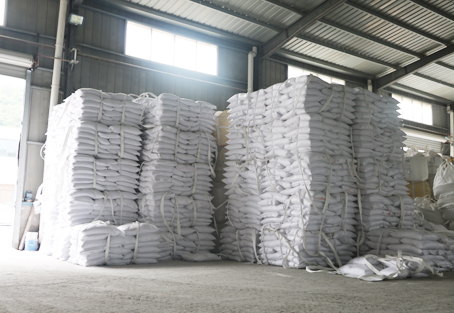